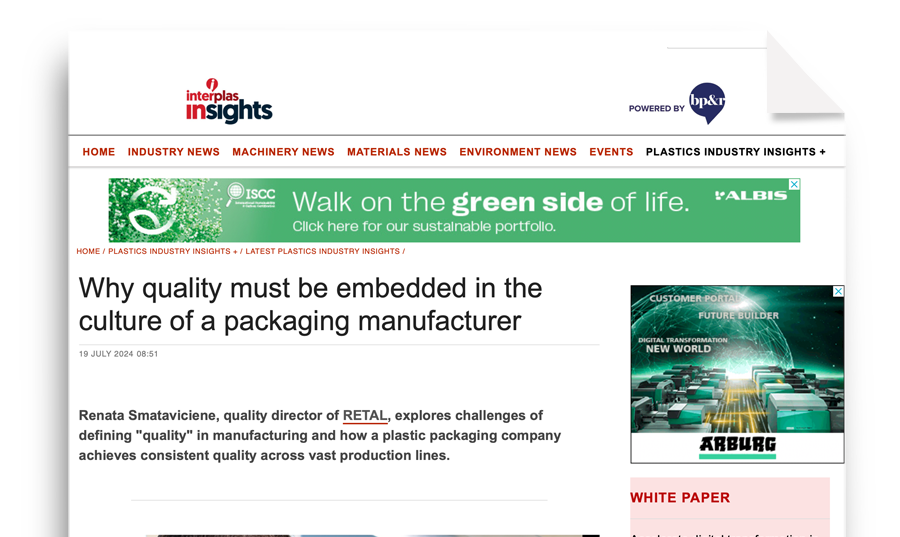
Renata Smataviciene, quality director of RETAL, explores challenges of defining "quality" in manufacturing and how a plastic packaging company achieves consistent quality across vast production lines.
There is no legal definition of the word ‘quality’; it gets used easily even though it’s hard to achieve. For manufacturing businesses, producing products of quality doesn’t happen by accident. It can only happen when the importance of quality is embedded into the culture.
But how can quality be embedded into the culture when there is no legal definition of what quality means? Who decides what a good quality product actually is, and how can ‘quality’ be defined across a large company with myriad departments, all contributing to a finished product?
The short answer is, with great difficulty! The longer answer, according to experienced quality director Renata Smataviciene, is somewhat more involved. Smataviciene explains how repeatedly achieving quality is a long-term, layered approach that requires clarity, tenacity and great attention to detail, as well as the careful recruitment, training and supervision of skilled people. She said: “Working in global production means that quality must underpin everything we do. It’s not a ‘one and done’ situation; we never take quality for granted and appreciate that it’s a constant process of checking, testing and learning.”
Smataviciene is the quality director for multinational plastic packaging producer RETAL in the EU and US and has responsibility for the quality of over 800 SKUs produced on over 170 state-of-the-art production lines, producing 13.41 billion preforms operated by more than 1600 skilled workers in 2023. That’s a lot of ducks to get in a row.
“We produce preforms and closures for many of the world’s leading food and beverage brands,” added Smataviciene, “so quality must come first. Our customers have very high expectations, and we have to meet those expectations every single time. This is where the definition of quality comes in, as it is crucial that we know exactly what those high expectations are. Our teams take time to clarify precisely what each customer needs; nothing is left to chance. We ask the right questions to get the information needed, then it is up to me and my team to guarantee that the quality expected is delivered.”
To achieve this, Smataviciene and her team have a sophisticated system of quality control, supported by a range of technological tools, with each RETAL location achieving the same quality assurance. She continued: “Our customers are global, so our products must meet the same quality standards for each different market; standardised quality allows for brand owners to be reassured. Our quality control is the same at each facility thanks to our detailed verification process. The fulfilment can be different depending on the product and the specific equipment, but each step is verified according to the quality and process performance required.”
The elements that can vary include the materials used, the volume of recycled material, additives, and the required weight of the preform. Smataviciene is clear that the role of sustainability in quality control is increasingly important, particularly when working with global brands that are driven to offer consumers the most responsible packaging possible. “Recycled material usage is so important now, we’re continually working with our customers and our designers to understand how best to implement progressive sustainable solutions. Sustainability must always be the focus, but through the lens of quality. Our quality never reduces, even when our weights reduce and our volumes of rPET increase. Tethered closures also bring with them new testing, new production challenges, but ultimately these are our problems to solve, which we always do. We bring solutions.”
This commitment to bringing solutions is where the culture of quality is most evident. Only with detailed and repeated feedback can a culture of quality be embedded, especially when the team is located across factories, countries and time zones. Smataviciene concluded: “A culture that expects quality has to be supportive and transparent. Sharing best practice is expected. Training is intense and visits are regular. We have to learn quickly from any non-conformities. It’s about checking and checking again, every process and every product. It’s about lists and more lists! Nothing happens by accident. We audit everything and we’re always learning.”
Read online at Interplas Insights