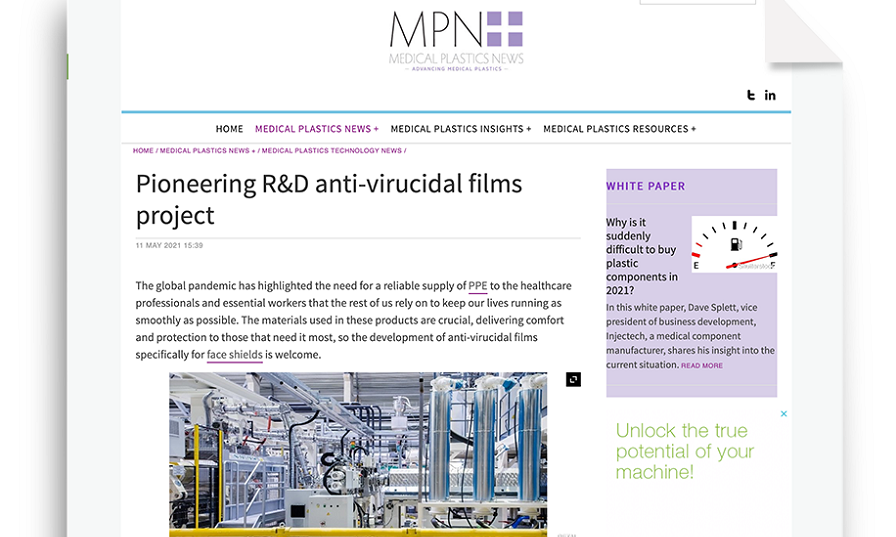
The global pandemic has highlighted the need for a reliable supply of PPE to the healthcare professionals and essential workers that the rest of us rely on to keep our lives running as smoothly as possible. The materials used in these products are crucial, delivering comfort and protection to those that need it most, so the development of anti-virucidal films specifically for face shields is welcome.
As the understanding of COVID-19 evolves, the demand for products that support essential workers at this time are changing too, particularly as the wider public is largely ready to get back to the ‘old normal’ now that we’ve had enough of the ‘new normal’. Reliable, practical PPE has been in incredible demand over the past year, and this is likely to continue, as our appreciation for how quickly a virus can have such a devastating impact on our daily lives is evident.
Although the initial scrabble of face masks and hand sanitiser has passed, we now see a great opportunity for the development of added value PPE that deliver on more than just emergency care. Rather, there is a chance to make keeping our essential workers safer in greater comfort.
One such project is the development of plastic film for face and eye shields with anti-virucidal properties integrated into the film at RETAL Baltic Films, which has recently gained funding from the European Union Funds Investment Operational Programme under its ‘aid for tangible investments in COVID-19 R&D projects’ initiative.
The RETAL Baltic Films team prove the potential benefits of a plastic film with anti-virucidal properties in the complex epidemiological situation regarding the spread of the SARS-CoV-2 virus and the incidence of COVID-19 specifically with regard to the protection of medical staff.
General manager Viktorija Griziene explains: “In the early days of the pandemic we quickly modified our existing APET film for food and beverage applications so it could be used for face shields, which we happily donated for the production of face shields and now also produce commercially. We have integrated an anti-fog capability which is highly appreciated by essential workers who often have to wear their masks for many hours at a time, so the transparency and anti-fog aspects are crucial. We are now working on taking our face shield film to the next level by integrating anti-virucidal properties to give an additional level of protection.”
Read full-text article online at Medical Plastics News