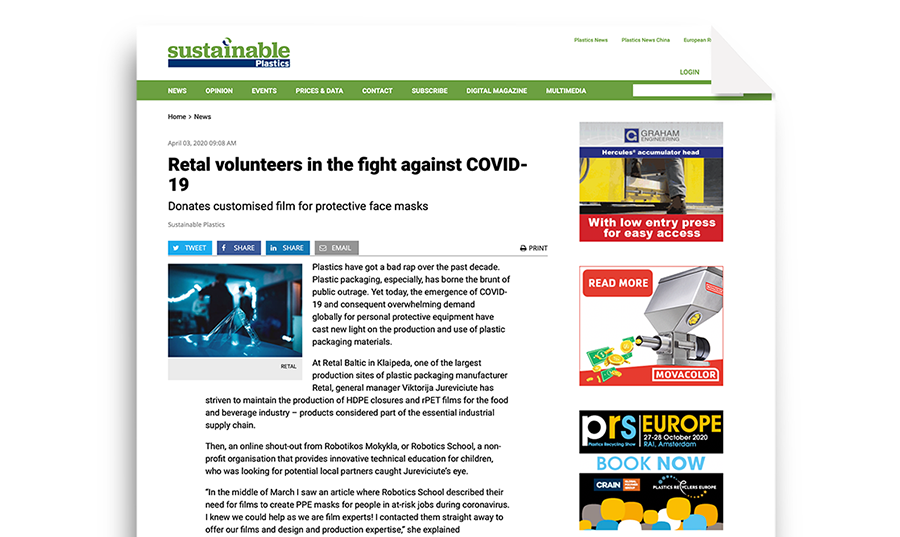
At Retal Baltic in Klaipeda, one of the largest production sites of plastic packaging manufacturer Retal, general manager Viktorija Jureviciute has striven to maintain the production of HDPE closures and rPET films for the food and beverage industry – products considered part of the essential industrial supply chain.
Then, an online shout-out from Robotikos Mokykla, or Robotics School, a non-profit organisation that provides innovative technical education for children, who was looking for potential local partners caught Jureviciute’s eye.
“With a few production changes, we could offer exactly what the front-line workers needed. Even though this pandemic has been an incredibly busy and challenging time for everyone, our team really pulled together to produce the film required – everyone was really motivated to help.”
The Retal Baltic production team first assessed its current film production to see how it could be adjusted to meet the performance for the masks. A few trials were carried out to decide which thickness would be suitable, with a one-layer film with anti-block additives chosen as it offers the clearest view. “We tested our GPET film too, but APET was already good enough and allowed for a peel-off cover if needed,” said Viktorija.
With the wholehearted support of the production teams and by slightly adapting its normal production over the weekend, Retal swung into action.
“We've been able to produce enough of the right film for 70,000 masks, which we've happily donated to Robotics School,” said Jureviciute.
The Robotics School team is coordinating volunteers for cutting the masks with lasers as well as their collection and delivery; libraries are 3D-printing the frames used with the Retal film masks for medical workers.
The film PPE masks are being distributed to ambulance workers, medical services staff and hospitals, as well as increasingly to production staff in industrial companies. With more people than ever before needing to use reliable PPE masks in order to continue to perform their work safely, Retal is delighted to be able to offer the necessary skills and resources, said Jureviciute.