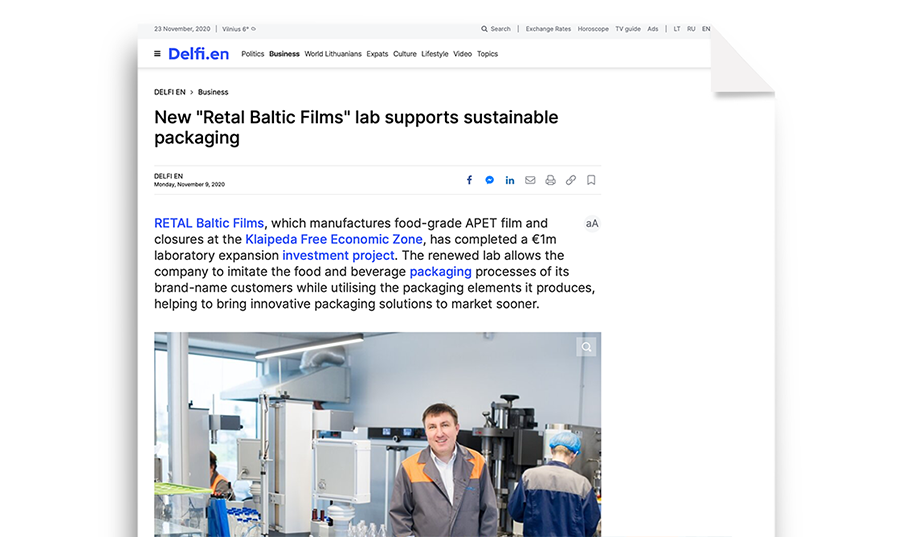
RETAL Baltic Films, which manufactures food-grade APET film and closures at the Klaipeda Free Economic Zone, has completed a €1m laboratory expansion investment project. The renewed lab allows the company to imitate the food and beverage packaging processes of its brand-name customers while utilising the packaging elements it produces, helping to bring innovative packaging solutions to market sooner.
The company has been pursuing scientific research and production testing projects in Klaipėda since 2016, during which time its laboratory has been certified by one of the world’s largest beverage producers. The current R&D capacities of the company have allowed it to successfully perform tethered cap research and to create and test the product, in turn contributing to a greater quantity of packaging elements being returned for recycling and meeting the EU Directive on single use plastics.
Believing in the lab’s importance and its contribution in developing more sustainable products for the market, the company decided to expand its R&D capacity, prompting the completion of the expansion of the laboratory’s premises and purchasing new laboratory equipment this year. The company will transport a full set of equipment to Klaipeda and install it by the second quarter of 2021. Currently, the laboratory premises and equipment have drawn €1m investment, and since 2016, €800K has been allocated for purchasing the equipment. The company plans to purchase a further €700K worth of laboratory equipment. General Manager at the company Viktorija Grižienė notes that the new laboratory will allow the company to expand its research into closures and will open up totally new opportunities in the food film segment. “In terms of bottle closures, we already are a research centre for our global group, and we have also established firm partnerships with third parties. The entire world is keen to use more recycled and sustainable materials in bottle caps and bottle preforms, and in our new lab we can test every idea and possibility by imitating the entire packaging process, replicating the conditions and technologies of our clients. Today, most of the food packaging on the market is comprised of components supplied from various manufacturers, which does not ensure optimal compatibility, functionality, sustainability and opportunities to improve the packaging. We can create products for our customers which are more optimal, more sustainable and easier to recycle,” V. Grižienė says.
Read more at Delfi.lt